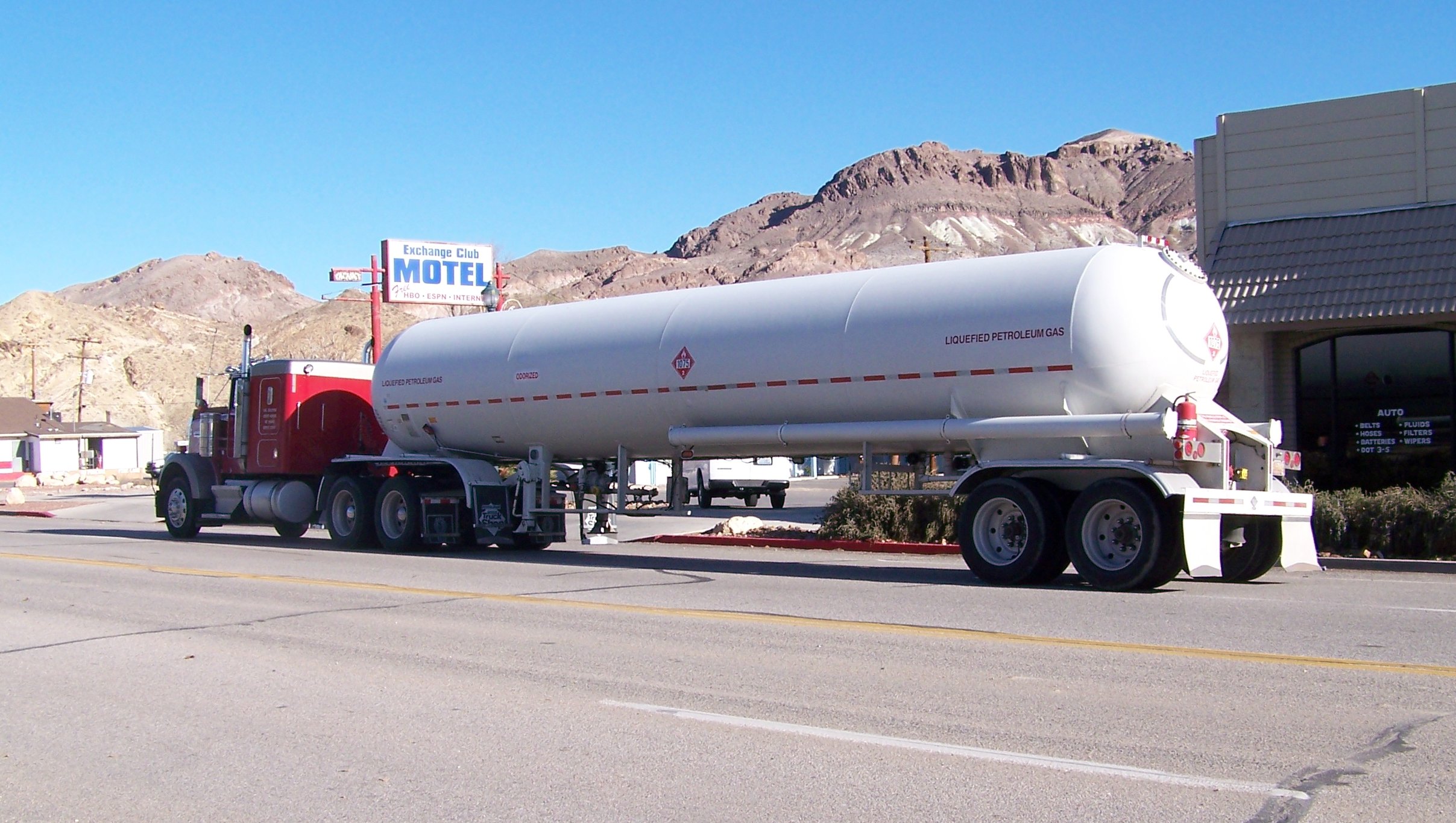
B620-09 Services For Industrial Hose In
Ontario & Across Canada
Introduction
At Ontario Hose, we offer comprehensive B620-09 services to ensure your company’s hoses comply with the stringent requirements of the B620-09 standard. Our services include training, certification, and testing, providing you with the assurance that your hoses meet the highest safety and performance standards.
What is B620-09?
Our B620-09 Services
Training
Certification
Testing

Benefits of Our B620-09 Services
Enhanced Safety: Ensure that your hoses meet the highest safety standards, reducing the risk of accidents and failures. Regulatory Compliance: Meet all necessary regulatory requirements for the transportation of dangerous goods.
Improved Performance: Our testing and certification processes ensure that your hoses perform reliably under demanding conditions. Expert Training: Equip your team with the knowledge and skills needed to maintain compliance and safety.
Our B620-09 Compliance Process
- Initial Consultation: We assess your current hoses and identify areas that need improvement to meet the B620-09 standard.
- Training: We provide comprehensive training for your staff on the requirements and best practices for B620-09 compliance.
- Testing: We conduct rigorous tests on your hoses to ensure they meet the necessary standards.
- Certification: We provide certification for hoses that meet the B620-09 requirements, giving you documented proof of compliance.
- Ongoing Support: We offer ongoing support and re-certification services to ensure continued compliance and safety.
Frequently Asked Questions
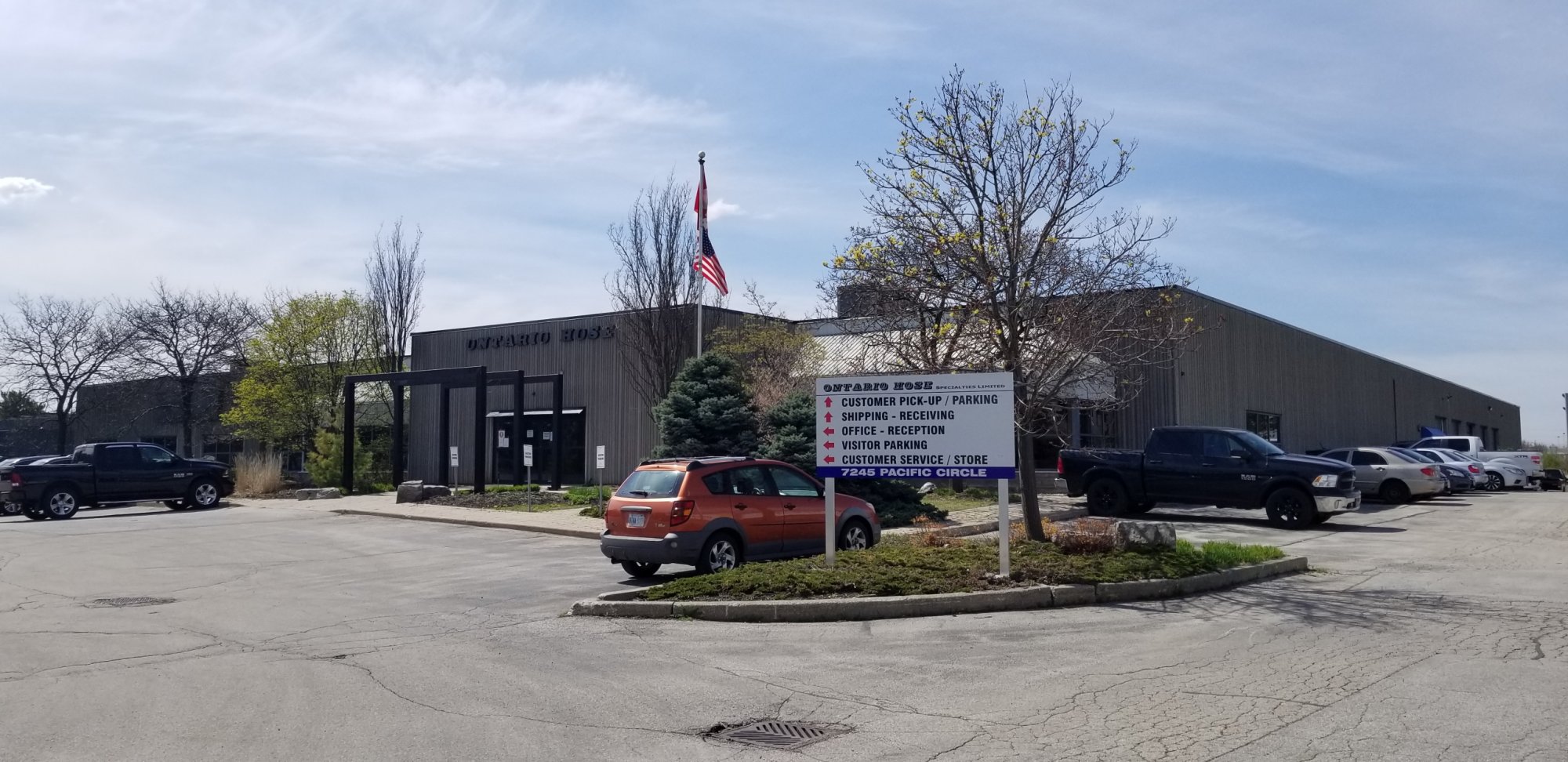
Contact Us for B620-09 Services
- Phone: (905) 670-0113
- Email: webstore@ontariohose.com